Modular and prefabricated construction has gained popularity in recent years and construction materials shortages are further poised to elevate the sector, according to executives in the space.
Subscribe to the Crunchbase Daily
Startups in the construction space have raised nearly $1.5 billion so far this year, more than the nearly $1.2 billion the sector raised in all of 2020, per Crunchbase data. Companies focused on building materials specifically have raised more than $430 million this year, per Crunchbase data, with Prescient’s $190 million funding round leading the pack in May, followed by Veev’s $100 million round in March.
The main reason for these new ways of building is clear: There’s a very real housing shortage in the United States, and it’s only gotten worse since the COVID-19 pandemic hit, disrupting supply chains and impacting the construction industry as some projects were paused.
According to mortgage loan company Freddie Mac, the shortage of U.S. homes to meet demand has grown by 52 percent from 2.5 million homes in 2018 to 3.8 million in 2020, with that figure expected to rise. Demand is going up, especially with low interest rates that encourage homebuying, per Freddie Mac.
To add to the problem, many homes in the U.S. were built 70-some years ago, and are due to be rebuilt for one reason or another, according to Amit Haller, CEO of Veev, which builds prefabricated multifamily homes and accessory dwelling units using primarily steel and other alternative materials.
Additionally, there’s a shortage of skilled labor, with only so many people who are able to build homes the way they’ve traditionally been built, he said.
“Not only do we have so much to catch up, we have so much to rebuild,” Haller said. “That means one thing: it’s a nonlinear problem. This problem requires a lot of disruption in construction.”
That’s prompted a lot of new startups in the homebuilding space to spring up, including some that use alternative materials to build homes and others that use tech to streamline the building process. While they’ve been more in the spotlight recently as the construction industry has faced a materials shortage and the lumber shortage has received the most attention, there’s also been shortages in other areas such as copper and windows.
Some of the recently funded companies in the construction tech space include Veev, which raised $100 million in March, and Mighty Buildings, which uses 3D printing to build prefab homes using materials including synthetic stone and raised $40 million in February.
The continued venture investment in the space came even as the most highly funded construction technology startup in the world, Katerra, was headed for implosion. The startup had raised at least $1.6 billion in known venture funding, mostly from SoftBank, but filed for Chapter 11 bankruptcy protection on Sunday.
The price of construction commodities including lumber and gypsum are the latest pressure point on the industry, which has been trying to find new ways to increase productivity, decrease cost and increase sustainability, according to Kathleen Egan, CEO of construction tech company Ecomedes.
Lumber prices spiked at the beginning of the pandemic, according to Salman Ahmad, CEO of construction tech company Mosaic Building. Although those prices finally dipped somewhat last week, they’re still up 300 percent year over year, according to the National Association of Home Builders. And a record number of builders reported material shortages last month, according to the association.
Companies such as Veev that use alternative materials have been less affected. Veev, for example, uses mostly steel instead of lumber, and uses high-performance surfaces rather than drywall. The company hasn’t been impacted significantly by the materials shortages, Haller said.
Modular home builders in the public markets are also on a tear. The stock price of Skyline Champion, for example, has increased by 102 percent over the past year.
Prefabricated home building involves manufacturing the parts of the structure offsite, while modular construction is a form of prefab construction involving the assembly of whole sections offsite and assembling them onsite.
A person’s home is the largest, most expensive and most-used consumer product, Haller said. Homes aren’t often seen as a consumer product, according to Haller, but they are one in a way. And just like a consumer would want to buy a new phone with the latest camera, the same goes for home technology, he said.
“Once you start to think about the home as a product, you have to ask yourself questions about usability and sustainability. Is it the latest and greatest technology?” Haller said.
There’s always been a bit of curiosity in alternative materials in the construction industry, but there’s been a renewed interest as people look at how technology can make the construction industry more efficient, according to Ahmad.
“I think there’s some acceleration of that than what you’ve seen historically, and I think there’s a renewed interest in that candidly with where lumber pricing is today.”
Illustration: Dom Guzman
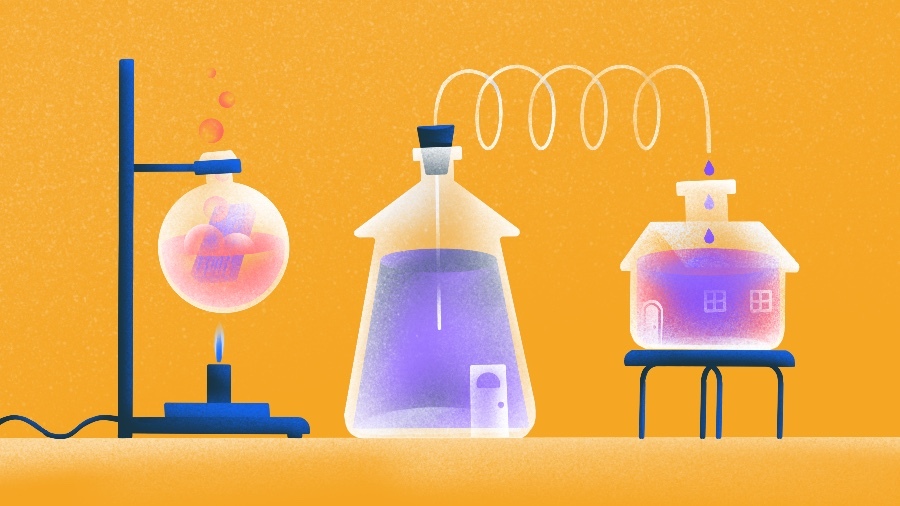
Stay up to date with recent funding rounds, acquisitions, and more with the Crunchbase Daily.
67.1K Followers